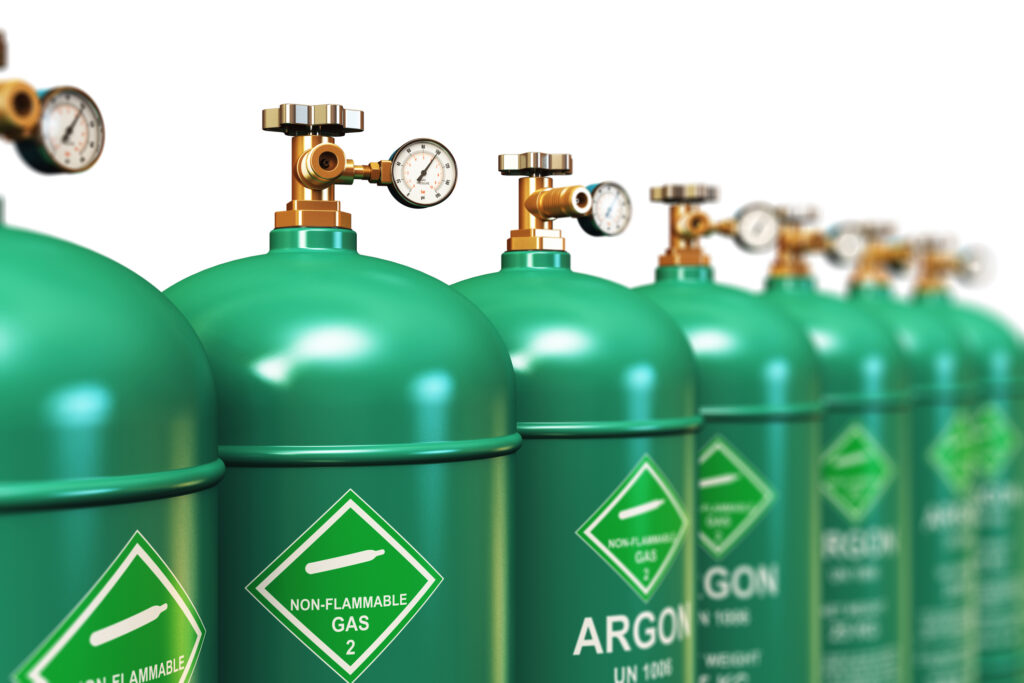
The Argon Advantage in Additive Manufacturing
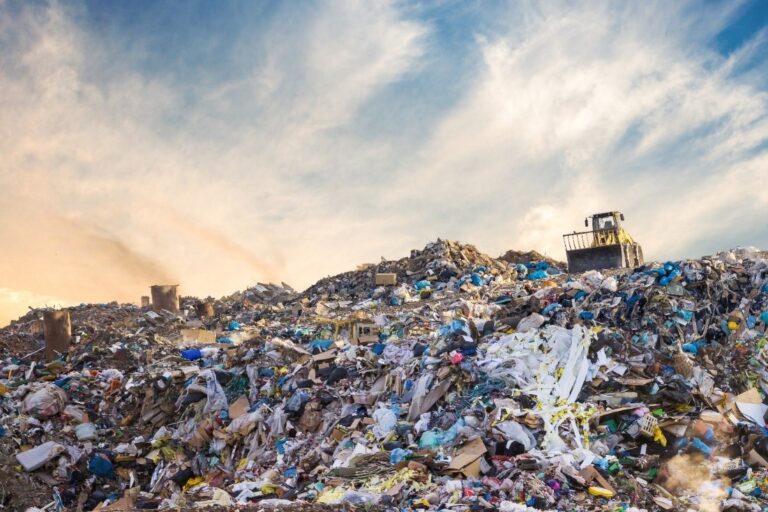
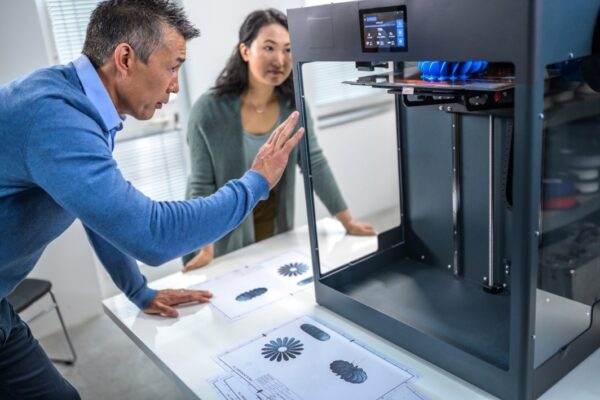
3D printing works by fusing polymer, ceramic, and even metal powders layer by layer. It began as a way to rapidly prototype models, but it has been improved to the point of creating functional components. Most of the powders even come from manufacturing remnants, so 3D printing repurposes what would otherwise be wasted! To create durable, defect-free components, high-end 3D printers utilize an inert-build chamber where air is displaced by an inert gas to remove moisture and prevent corrosion and oxidization of the materials. Different inert gases have their strengths, and when it comes to creating metal components, like those that would be needed in many manufacturing capacities, one inert gas is a standout.
Enter argon. It is prized for being noncombustible, denser than air (and therefore able to displace it), and chemically unreactive (inert) under most conditions. Its chemical structure minimizes the transfer of heat, vibrations, and other energy, which gives it insulating properties. It gets its name from the Greek word for “lazy” or “inactive.”

Argon has a long history of use in metal manufacturing outside of 3D printing. It is used in the creation of stainless steel and other high-end alloys. Stainless steel gets its unique corrosion resistance and hardness from a combination of chromium and a low carbon content. In a process called argon oxygen decarburization, oxygen is injected into molten steel to remove carbon by forming carbon monoxide, while argon mitigates chromium loss and protects the iron in steel from the corrosive effects of the oxygen. Stainless steel is considered a green material because it does not leach dangerous chemicals as readily as plastic, and is entirely recyclable. In fact, around 80% of stainless steel items get recycled, whereas less than 9% of plastics are.
Another common use for argon is MIG (metal inert gas) and TIG (tungsten inert gas) welding. Argon acts as a shield gas to prevent contamination of the welding surfaces by displacing air and moisture. It also plays a role in stabilizing and shaping the penetration profile of the arc. This helps ensure the integrity of the weld, which encourages first-time quality.
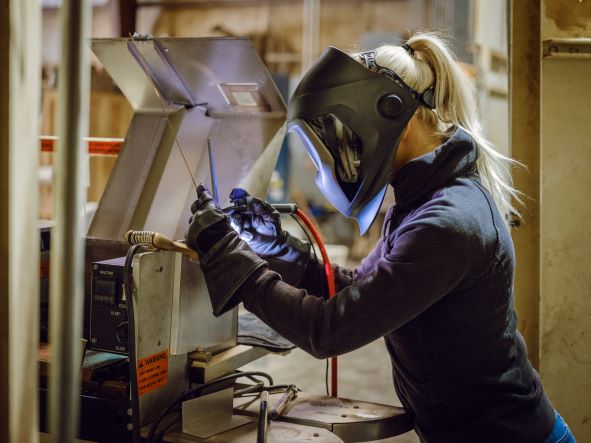
Argon can be found in several other applications as well, as an insulator or a natural means for preservation:
- Argon is fully transparent, prevents moisture buildup, and increases energy efficiency when compared to air, making it an ideal filler for double-paned windows.
- When used to fill diving drysuits, argon prevents loss of body heat for the diver and resists higher pressures than atmospheric air, allowing for deeper dives.
- Since nitrogen and argon are non-toxic and found naturally in the air we breathe, they are a safe means to preserve food and beverages from the degrading effects of oxygen without the health concerns of added chemical preservatives. This is important because it is estimated that between thirty and forty percent of all food produced in the United States is discarded, which results in a significant waste of resources. Nitrogen is more commonly used in packages that come sealed from manufacturers, but argon is often used in high-end restaurants to displace oxygen in opened wine, beer, and spirits containers to preserve the quality of the beverage.
- Argon can be added to medical ventilation to protect the brain after experiencing oxygen deprivation, and it can also help treat heart arrhythmia.
- Argon lasers can remove tumors, provide retinal phototherapy, and can even repair damaged arteries.
- Incandescent and fluorescent builds are filled with argon to prolong filament life. In decorative lighting, neon produces a red-orange color, helium glows yellow or orange, and argon glows with a blue or violet light.
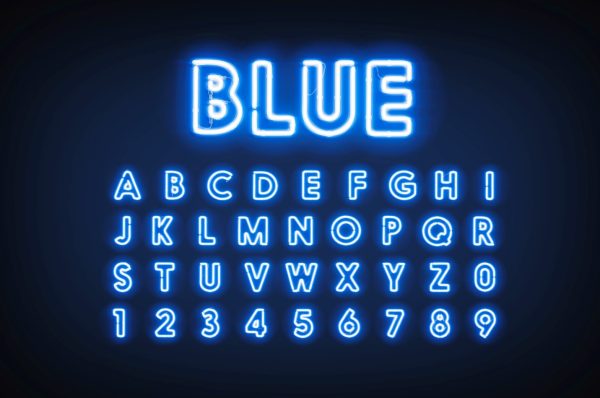
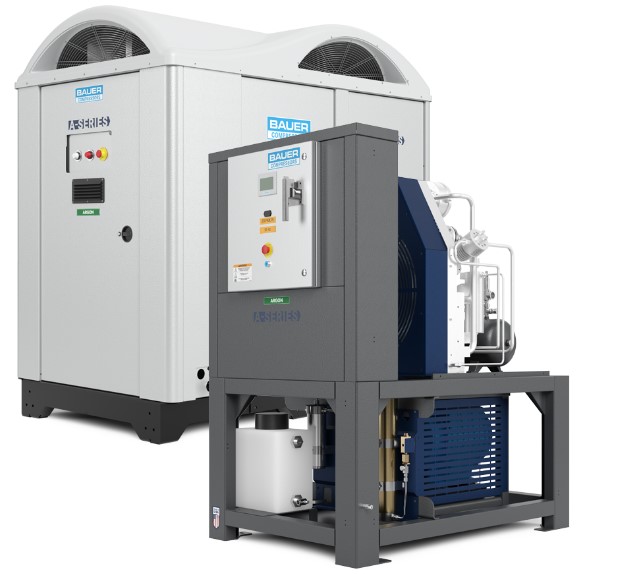
The Ar-Series by BAUER Compressors is designed to handle the high pressures required for argon compression, and we have multiple compressor options that can integrate into argon recovery. We also manufacture boosters to increase pressure after filtration for bottling the purified argon. We have 5-20 horsepower compressors for applications where a small amount of gas is used, or in applications with argon gas mixtures, and 50+ horsepower compressors for larger applications. All our compressors are designed and manufactured in-house in a vertically-integrated manufacturing process that eliminates waste at every step. Our compressors are the most durable and reliable on the market, which not only provides our customers with the lowest cost of ownership available, but it also saves resources that would be used to replace broken components or systems.
Over the past seven decades, BAUER has constantly innovated to meet the needs of our customers and has built a world-renowned reputation as the premier producer of breathing air, industrial air, helium, nitrogen, argon, and biogas compressors. BAUER is relentlessly pursuing ways in which we can be part of the solution for a better future for our customers and the planet. Check out how we’re playing a role in creating a clean energy source from a greenhouse gas that’s up to 80 times more dangerous than carbon dioxide!
1 thought on “The Argon Advantage in Additive Manufacturing”
Comments are closed.
Very interesting and informative!
I love seeing the innovation and positive impacts BAUER is making, and learning the “why” and “how” of the science that makes it all work.
I applaud their dedication, both to reducing their own impact on the environment, and to introducing greener options (and education about them) into the marketplace, so their customers can easily follow suite.